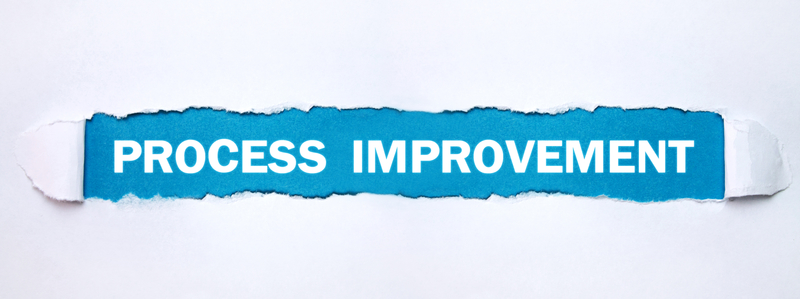
4 Myths About Process Improvement
Six Sigma is one of the most popular process improvement methodologies in the world, despite there be a number of them. However, process improvement itself is one term that many people have strong feelings about. Depending on how it is perceived, those feelings can range from good to bad. Ultimately, perceptions are influenced by what one has heard about process improvements.
This brings us to the myths that surround this concept. Many people know that when it is done correctly, optimizing a process to be better than it previously was can reap numerous benefits. Among these benefits is increased customer satisfaction and revenue. But some people are either reluctant to try out process improvement or want to try it for the wrong reasons because they have heard unhelpful myths.
Here are four myths that you will hear when it comes to process improvement and why you shouldn’t believe them.
1. There’s only one way to improve a process
Many industry professionals have one methodology of process improvement that they champion over others. But process improvement transcends such dogma. As mentioned earlier, there are a number of process improvement methodologies out there, including Six Sigma, Total Quality Management (TQM) and Toyota Production System (TPS).
The methodology you ultimately use depends on the process you are trying to improve. While the underlying principles of the methodologies are the same, the inner tools and techniques are different. There’s no one-size-fits-all methodology that you need to follow to make it a success.
2. Process Improvement is only for manufacturing
Since process improvement is popular in manufacturing, many people believe that is the only place where it belongs. Indeed, companies that champion process improvement include the likes of Toyota. But one does not need to have an assembly line if they wish to reap the benefits of process improvements.
In order to ascertain if a process can benefit from process improvement, you need to ask yourself if it creates value. If the answer is in the affirmative, then that process is a great candidate for improvement efforts. And doesn’t matter if you’re in the technology, health or non-profit sector.
3. You need to improve a process once
What happens after the process improvement efforts have become a success? Many organizations usually forget to make continuous improvement part of their organizational culture. This means people don’t know what to do after the process has been optimized. Eventually, the initial benefits are lost and the process can revert back to its former self.
Improvement is an ongoing process, and most methodologies usually stress this in the last step. While doing it once might sound like an attractive selling point, but without continuous improvements, the results won’t stick. Workers will no longer identify defects in processes and fix them to keep things running smoothly. You need to make sure that everyone, from the janitor to upper management, knows that continuous improvement is their responsibility.
4. Process improvement is time-consuming
Another myth that is often repeated about process improvement is that is a very slow process. When it comes to anything in an organization, it requires resources mainly time and money. This means that the longer something drags on, the more resources need to be poured into it. Thinking like this can make one dread undertaking process improvement, making it appear time-consuming and costly.
But saying process improvement is slow in and of itself is false. If an organization shows a strong commitment and drive to process improvement, it can be carried out pretty fast. Many organizations spend time on implementing specific methodologies instead of getting stakeholders on board and building the right team to push the agenda, even after it has succeeded. In the end, process improvement takes longer than it needs to.
If you want something to work for you, you have to know what is real about it and what is false. Unfortunately, even things like process improvement, with its proven track record of success, are not immune to fables. Luckily, with any false thing that is said about methods that produce positive results, the truth can be easy to uncover.
Become a Lean Six Sigma professional today!
Start your learning journey with Lean Six Sigma White Belt at NO COST
Leave a Reply